Unraveling the Enigma of Porosity in Welding: Tips for Reducing Problems and Taking Full Advantage Of Quality
In the intricate globe of welding, porosity remains a persistent obstacle that can significantly impact the quality and honesty of bonded joints. As we delve right into the depths of porosity in welding, discovering the secrets to its avoidance and control will certainly be paramount for professionals looking for to grasp the art of premium weldments.
Recognizing Porosity in Welding
Porosity in welding, a common concern experienced by welders, refers to the existence of gas pockets or voids in the welded material, which can endanger the honesty and top quality of the weld. These gas pockets are generally trapped throughout the welding procedure because of numerous variables such as improper securing gas, infected base products, or wrong welding parameters. The formation of porosity can compromise the weld, making it at risk to breaking and rust, ultimately bring about architectural failures.
By recognizing the value of maintaining appropriate gas shielding, making sure the sanitation of base materials, and enhancing welding settings, welders can substantially reduce the chance of porosity development. Generally, a comprehensive understanding of porosity in welding is important for welders to create premium and sturdy welds.
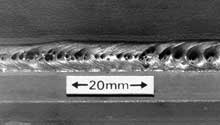
Usual Reasons of Porosity
When examining welding procedures for potential high quality concerns, understanding the usual causes of porosity is necessary for keeping weld integrity and protecting against structural failures. Porosity, identified by the visibility of cavities or voids in the weld steel, can considerably endanger the mechanical residential properties of a welded joint.
Furthermore, welding at inappropriate parameters, such as excessively high traveling rates or currents, can create excessive disturbance in the weld pool, capturing gases and causing porosity. By resolving these usual causes through correct gas securing, product prep work, and adherence to ideal welding parameters, welders can minimize porosity and boost the high quality of their welds.
Strategies for Porosity Prevention
Executing reliable preventive procedures is vital in lessening the event of porosity in welding processes. One strategy for porosity prevention is ensuring proper cleaning of the base metal prior to welding. Impurities such as oil, oil, corrosion, and paint can lead to porosity, so detailed cleaning resource making use of ideal solvents or mechanical methods is vital.

One more trick precautionary step is the selection of the appropriate welding consumables. Making use of high-quality filler materials and protecting gases that appropriate for the base steel and welding process can substantially lower the risk of porosity. In addition, preserving correct welding parameters, such as voltage, existing, take a trip speed, and gas flow price, is important for porosity avoidance. Departing from the recommended settings can result in incorrect gas insurance coverage and poor fusion, leading to porosity.
Furthermore, employing appropriate welding methods, such as keeping a constant travel rate, electrode angle, and arc size, can help protect against porosity (What is Porosity). Adequate training of welders to guarantee they adhere to best techniques and quality control procedures is likewise crucial in reducing porosity flaws in welding

Best Practices for Top Quality Welds
One secret technique is maintaining appropriate tidiness in the welding location. Thoroughly cleaning up the work surface and surrounding area prior to welding can aid reduce these problems.
An additional ideal practice is to very carefully select the proper welding specifications for the particular products being signed up with. Correct parameter choice ensures ideal weld penetration, fusion, and overall top quality. Using premium welding consumables, such as electrodes and filler metals, can significantly impact the final weld quality.
Value of Porosity Control
Porosity control plays a vital function in making sure the honesty and top quality of welding joints. Porosity, identified by the visibility of tooth cavities or voids within the weld metal, can considerably endanger the mechanical properties and architectural integrity of the weld. Too much porosity weakens the weld, making it more vulnerable to splitting, rust, and overall failure under functional lots.
Effective porosity control is crucial for maintaining the preferred mechanical buildings, such as stamina, ductility, and durability, of the welded joint. What is Porosity. By minimizing porosity, welders can enhance the overall high quality and integrity of the weld, making sure that link it meets the performance demands of the designated application
Furthermore, porosity control is essential for accomplishing the preferred aesthetic appearance of the weld. Extreme porosity not just compromises the weld yet additionally takes away from its aesthetic allure, which can be important in sectors where appearances are necessary. Correct porosity control methods, such as utilizing the appropriate protecting gas, controlling the welding parameters, and guaranteeing proper sanitation of the base materials, are useful content crucial for producing high-grade welds with marginal defects.
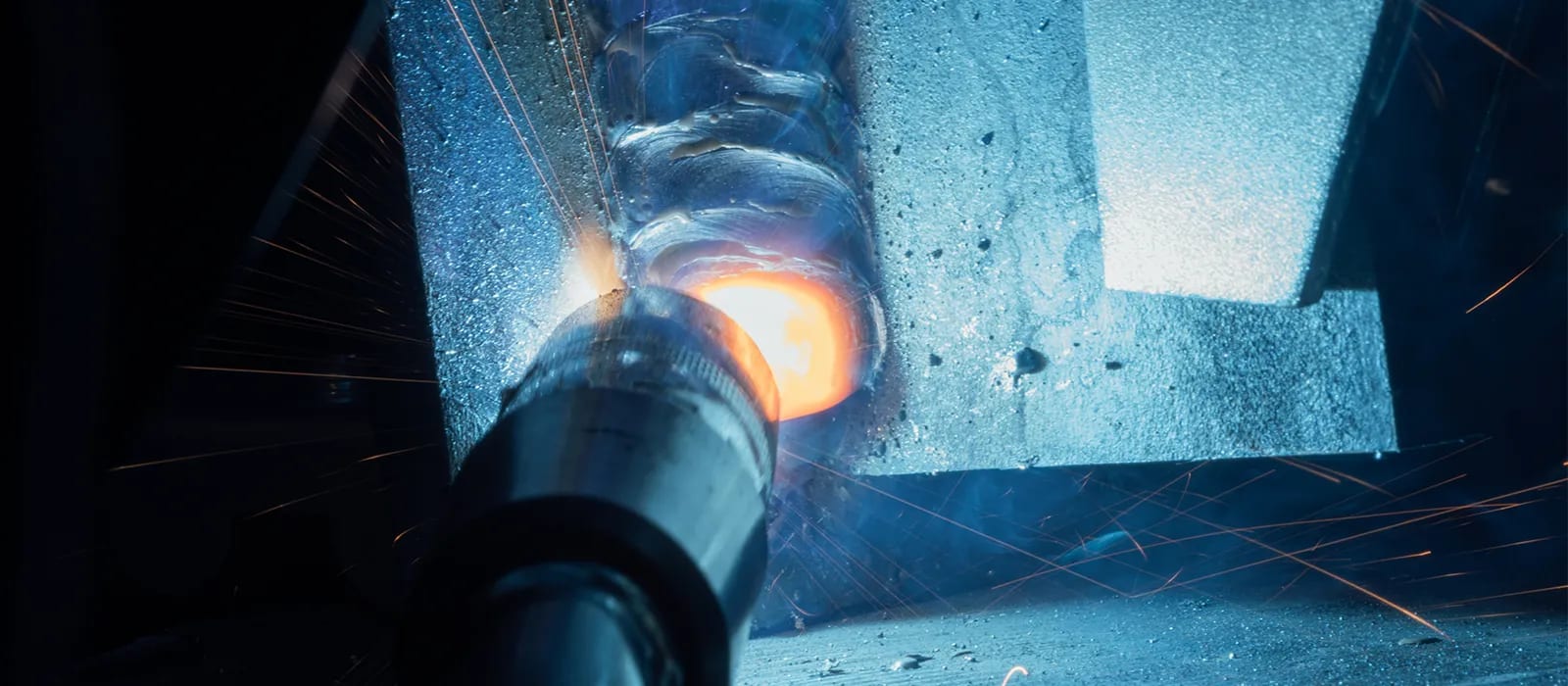
Conclusion
In conclusion, porosity in welding is a common defect that can endanger the quality of the weld. It is necessary to regulate porosity in welding to make sure the stability and strength of the last product.